How To Produce The Perfect Chip
When we machine metal of any kind, the chips – or swarf – give us clues about the efficiency of our cutting process. For example, early machinists noted that blue chips indicate heat is being properly dissipated, so the cut was going well. Blue swarf, therefore, were considered “perfect” chips.
Today there are more precise ways to optimize machine tool performance. One such method is the technology of Machining Dynamics that focuses on tool point or cutting tool behavior during the machining process. This technology is the basis for a system pioneered by a company called Blue Swarf. This method enables machinists to compensate for the inherent vibration and frequencies created during the machining process.
A Focus on Milling
According to Blue Swarf’s founders, Machine Dynamics focuses on milling because it involves a number of cutting teeth entering and exiting a workpiece throughout machining. These motions can create chatter that reduces cutting accuracy. In other operations, such as turning, drilling and boring, the cutting tool is in continuous contact with the workpiece, thereby lessening the impact.
There are actually two frequencies created during the milling process. Tooth Impact Frequency occurs when a cutting tool impacts the workpiece, and is determined by the number of teeth on the tool and the spindle speed. Tool Point Frequency involves the flexibility of the tool point, the number of times per second a tooth comes in contact with the workpiece, and the cutting forces applied by the tool for a specific depth and width of cut.
If these frequencies are compatible, each tooth impacts the workpiece at the same time, achieving uniform chip thickness. The cut is quiet, surface finish is smooth, the part is accurate and tool life is maximized.
If the timing is off and the next tooth arrives too late, it creates a larger than programmed chip load, causing the tool to deflect more and thus throwing off the timing of the next tooth. As a result, the tool will fail sooner and possibly scrape the part. Conversely, if the tooth arrives too early, it undercuts the programmed dimension and throws off the timing.
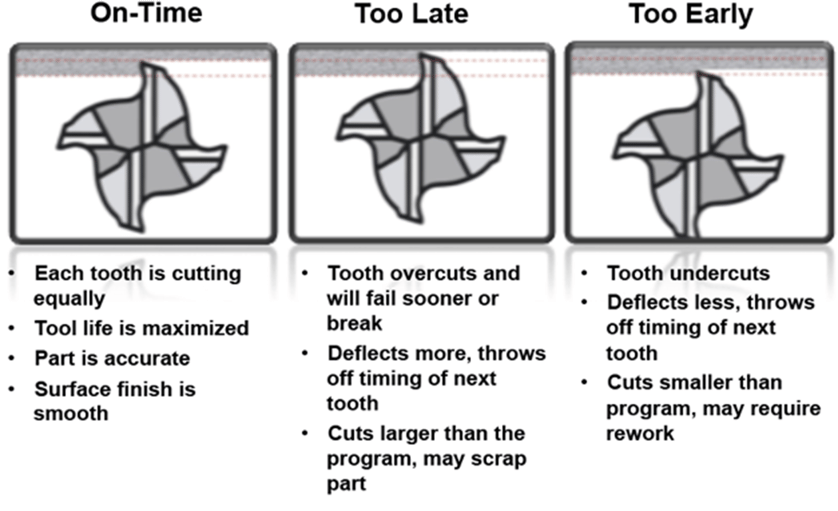
More Than the Cutting Tool
It would appear, then, that all you need to do is optimize the cutting tool impact timing and all will be well any time you use that particular cutting tool. However, the impact frequency involves more than just the cutting tool itself. No matter how rigid a machine tool may be, there are a number of parts involved in the cutting process that impact the accuracy of a cut: The cutting tool, the tool holder, the collet, the spindle, spindle bearings and the motion of the headstock. All of these have some degree of play that results in deflection of the cutting tool as it impacts the workpiece.
Moreover, as these combinations of components change, for example when you take a cutting tool from one machine to another, the frequencies also change because the other components will not be the same. Blue Swarf research indicates that there are over 4.8 quadrillion (4,800,000,000,000,000) possible combinations of machines, tools, tool holders and materials, each of which have their own frequencies.
Another factor that impacts frequencies is the number of cutting tool teeth. As the chart below illustrates, the number of impacts per second increases with the number of teeth. At 7500 RPM spindle speed, these vary from 250 Hz to 750 Hz per second.

The Blue Swarf Solution
Because there are so many variables that contribute to chatter, there is no easy way to make the necessary adjustments to minimize chatter. Through trial and error you can attempt to improve the situation by adjusting spindle speeds and trying various cutting tools and tool holder combinations, but the time investment is enormous and, odds are, you’ll never achieve the ideal result.
Blue Swarf enables you to dial in your milling process by using a simple tap test:

This Internet-based “stability improvement technology” uses a special hammer equipped with a transducer to tap the tool and holder assembly mounted in the machine tool. The hammer device records the frequency response for the unique tool, holder, spindle and machine combination. This data is encrypted and sent through the Internet for analysis. The result is posted to a dashboard that the machine operators can view on their computer screens, and which graphically presents the precise stable speeds, feed rates, width and depth of cut for optimum operation.
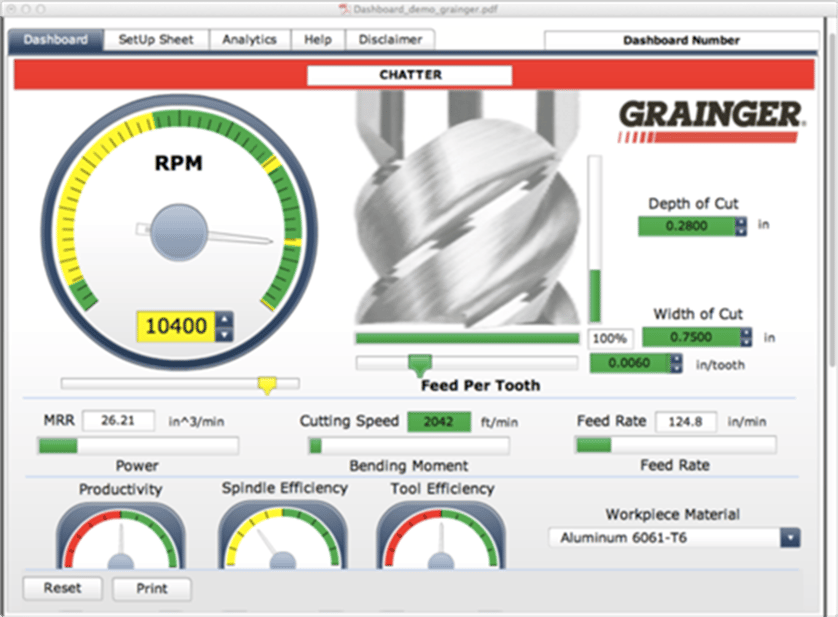
View the Blue Swarf Video
Visit the Blue Swarf Website to learn more about this unique technology and watch a video presentation on the subject. Or contact the applications experts at Gosiger for this and other ways to maximize your machine tool performance.
The above illustrations provided and copyrighted by Blue Swarf LLC