Automation Kicks up Productivity for High-Volume CNC Machine Shop
Posted by
Mike Williams on Tue, Mar 06, 2012
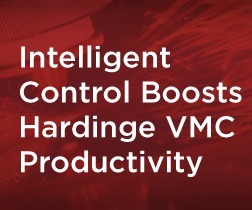
DGP, Inc. is a medium-volume Tulsa, Oklahoma CNC machine shop with key customers in the oil exploration and production industry. Among other products, the company makes a family of three control valve components for one customer at the rate of 900 – 1200 pieces per month. Owner Jay Taylor surmised that he could reduce his cost-per-part by automating the process. But what was the best approach, and how could it be accomplished most cost-effectively? For the answers he turned to Gosiger Factory Automation.
According to Taylor,
“This new setup boosts overall productivity by about 22%. By that I mean that the machine operator now produces between 20% and 25% more parts per shift than before. Although the cycle time is now actually 15 seconds longer than before we automated, by making consistently better use of the operator’s time we actually produce up to 25% more parts at the end of the shift. In addition, the entire process is now handled by one operator instead of two, which frees up the second operator to run another line.”
“The Gosiger people have been top notch to work with. The delivery and installation was as promised and whenever I have a question on the programming or some other issue I call one phone number and get the answer I need. I also can call them to bounce off ideas on other ways to improve throughput and productivity. They’re always helpful and professional.”
To learn how Gosiger used an Okuma lathe and THINC control, a proprietary pallet system and a Fanuc robot to boost DPG’s productivity, read the full case study.